Solar panels have revolutionized the way we harness energy, offering an eco-friendly alternative to fossil fuels. The intricate process of solar panel manufacturing involves several specialized steps, ensuring that each panel meets high standards of efficiency and durability.
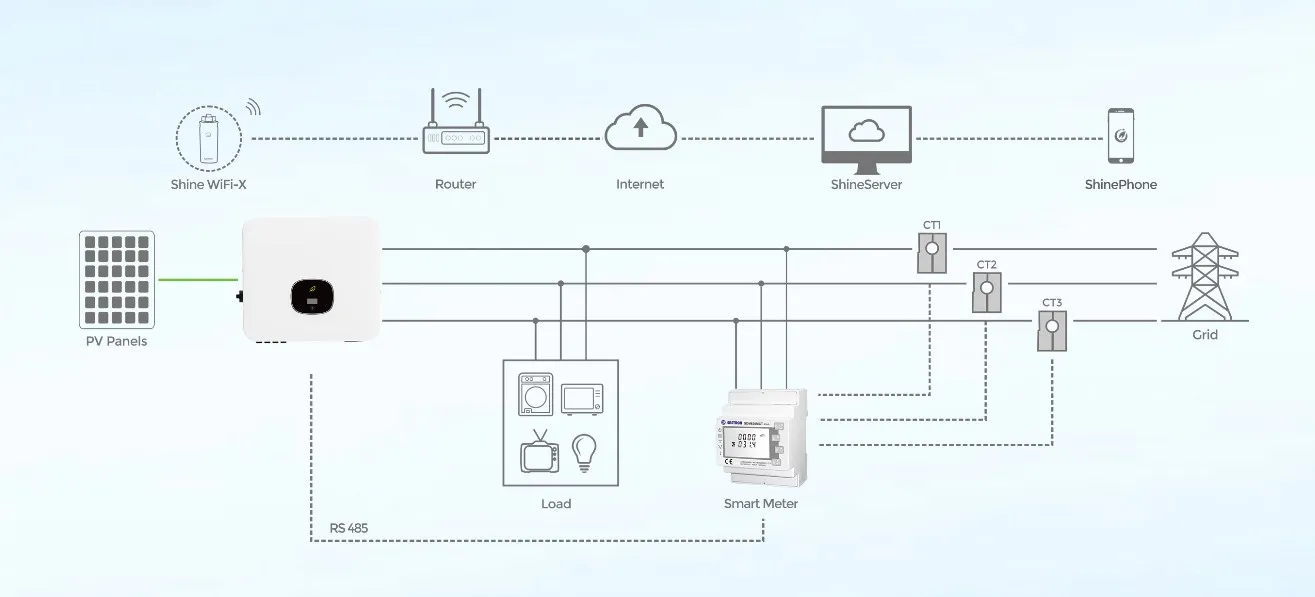
The journey begins with the mining of silicon, the primary component of most solar panels. Silicon is extracted from silica, a compound found in sand. Once procured, the silicon undergoes a purification process. This is crucial because the presence of impurities could significantly impact the efficiency of solar panels. The purified silicon is then cast into ingots, large cylindrical blocks, using the Czochralski method. This method involves placing a small seed crystal in molten silicon and slowly pulling it out to form a single crystal ingot.
Once the ingots are cooled and solidified, they are sliced into thin wafers using a wire saw. These wafers, just a fraction of a millimeter thick, form the foundation of the solar cells. Each wafer undergoes a thorough cleaning and polishing process to prepare it for the subsequent steps. This meticulous preparation is essential to ensure maximum solar energy absorption.
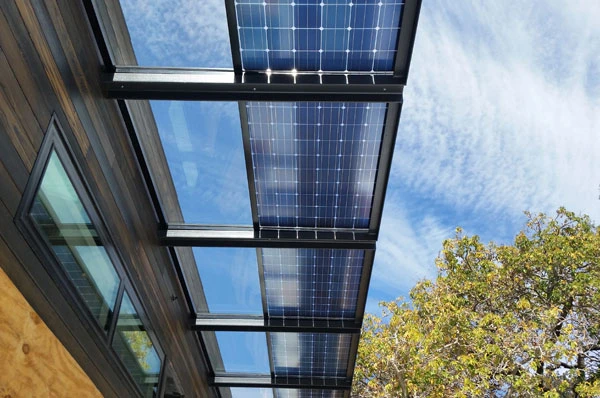
Doping, a process of adding specific impurities, follows. Phosphorus and boron are typically used to create a positive-negative junction, vital for the photovoltaic effect. This effect is the core of solar energy conversion, enabling solar cells to generate electricity. The doped wafers are then subjected to an etching process, which increases the surface area and further enhances energy absorption.
To protect the delicate silicon structure, an anti-reflective coating is applied. This layer not only minimizes the loss of sunlight but also gives the solar panel its characteristic dark blue hue. Following this, thin metal lines, known as fingers and busbars, are printed onto the wafer surface using a technique akin to screen printing. These metallic grids play a critical role in conducting the captured solar energy, facilitating efficient electricity flow.
Subsequently, the solar cells are meticulously assembled into a grid layout to form the solar panel itself. The cells are interconnected using flat wires and encapsulated between sheets of durable, transparent materials such as EVA (ethylene-vinyl acetate) and back sheets to protect them from environmental damage. This encapsulation process is conducted in a vacuum, ensuring that no air bubbles or moisture can interfere with the panel’s performance.
solar panel how its made
After encapsulation, the panels are framed with robust, corrosion-resistant materials, often aluminum, providing structural integrity and making installation easier.
A crucial aspect of solar panel manufacturing is quality control. Each panel undergoes rigorous testing to ensure it meets the required efficiency standards and can withstand various environmental stresses. Simulated environmental tests include exposure to extreme temperatures, humidity, and ultraviolet radiation.
Modern advancements in manufacturing techniques have drastically improved the efficiency and lifespan of solar panels. PERC (Passivated Emitter and Rear Cell) technology is one such advancement, which involves additional layers that reflect unabsorbed sunlight back through the cell, maximizing energy capture. Likewise, bifacial panels, capturing sunlight from both sides, offer increased productivity, especially when installed in reflective environments.
Moreover, researchers continuously explore new materials like perovskites that promise even higher efficiencies at reduced costs. Integrating cutting-edge developments into solar panel design not only enhances their capability but also solidifies the authority and trustworthiness of manufacturers who adopt these innovations.
As solar technology continues to evolve, the industry is moving towards more sustainable production methods, reducing waste and energy consumption in the manufacturing process. This commitment not only reflects the expertise of industry leaders but also demonstrates a trustworthiness that consumers can rely on when choosing solar energy solutions.
In conclusion, the sophisticated process of manufacturing solar panels is a blend of material science, engineering precision, and innovative advancements. Understanding these processes reveals the expertise and dedication behind each solar panel, fostering greater trust and adoption as we transition towards renewable energy sources. As the industry continues to advance, solar panels stand as a testament to human ingenuity in the pursuit of a sustainable future.